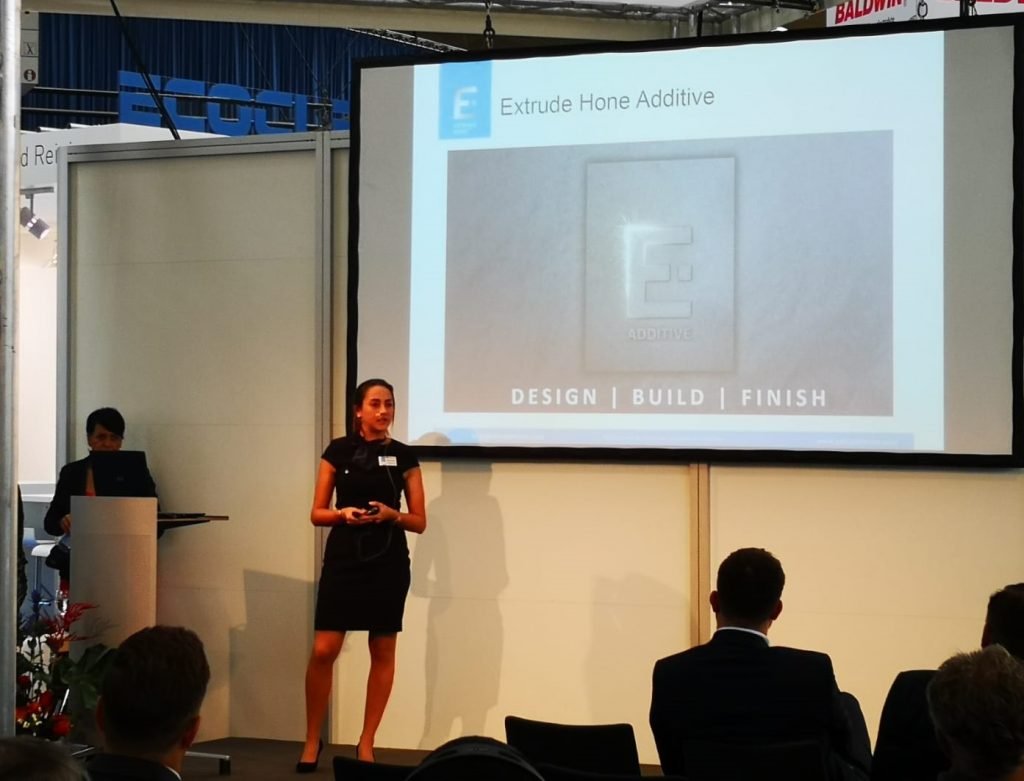
Extrude Hone presented at Deburring EXPO 2019’s first AM Theme Park.
A spot dedicated exclusively for the finishing of additive manufactured components.
The Deburring EXPO is the leading trade fair for deburring technologies and precision surfaces. It takes place every two years, and this was its 3rd edition. From October 8th to 10th, almost 200 Exhibitors and thousands of visitors from all over the world came to Karlsruhe, Germany.
The big innovation for 2019 was a space dedicated exclusively to the post-processing of AM components – metal Additive Manufacturing is growing and changing rapidly, and post-processing is challenging the industry.
We at Extrude Hone have many years of experience offering deburring, shaping and surface finishing solutions, and have tailored our technology around AM, also offering metal printing services thanks to in-house capability. Our direct experience in combining printing and finishing allows us to understand the post-processing issues from a genuine customer perspective.
From the removal of partially sintered material up to the improvement of very rough surfaces, Extrude Hone has a specific solution for its customers. The whole product portfolio was presented at the main booth, whereby real AM examples were highlighted inside our interactive “Hypebox” – the easiest way to learn how Extrude Hone technology works!
During the specialist forum, assisted by Fraunhofer IAPT AM experts, were we also actively engaged explaining how the TEM (Thermal Energy Method) technology is used to remove internal support structures, how we use AFM (Abrasive Flow Machining) to improve channel like complex surfaces and how COOLPULSE (ECM Electrochemical machining) is suitable to process simultaneously internal and external complex shapes.
On one side, the TEM process, well-known in the industry for deburring of conventionally manufactured components, is now capable of removing within a few seconds intricate support structures of 3D printed parts. Thanks to the combination of Engineering the controlled ignition during the process and the use of a pattern of the supports (generated by EOS’s software) it is possible to literally blow them away without causing any changes on part’s mechanical properties. Indeed, an added value solution for a real customer pain!
On the other side, AFM is the perfect fit to obtain high quality surfaces in complex internal channels such as those used for conformal cooling, filtration systems and fuel flow applications. Using a highly viscous, chemically inactive and non-corrosive media, surfaces and edges can be significantly improved, while maintaining the component’s geometry.
Completing our technology offering, COOLPULSE is a new and completely different technology suited to fast processing of both internal and external surfaces. It is based on the anodic metal dissolution principle (like Electro-Chemical Machining, and Electro Polishing), and uses a special, pH neutral and environmentally friendly electrolyte. The dissolution effect improves the surface of the part and removes material uniformly and consistently. The process can be simulated upfront and results optimized accordingly. This can also be achieved on features where forces should not be applied, as well as combining technologies to achieve the best results.
Extrude Hone Additive, our dedicated Business Unit for AM, offers superior solutions and provide customers with tailored post-processing strategy; we define customers’ needs and identify the main challenges starting from the design phase up to the finished product. By guaranteeing the best finishing results, we are positioning ourselves as a high-end one-stop-shop for the aerospace, medical, automotive and energy industries – and we commit every day to free engineer’s creativity from post-processing constraints.